Stein Dietrichson startet Re-Turn AS i 1998, og bedriften er i dag ledende på fagkompetanse innenfor plast. Nå er Dietrichson og Re-Turn sentrale i et nytt prosjekt som skal utvikle nye, sirkulære verdikjeder rundt gjenvinning av plast i Norge. – Plasten er en ressurs og den bør omdannes til noe fornuftig her i Norge i stedet for å bli eksportert, sier Dietrichson.
Re-Turn, som holder til i Fredrikstad, har et velutstyrt laboratorium og har spesialisert seg på laboratorietjenester, konsulentoppdrag og produktutvikling for kompositt- og polymerindustrien i inn- og utland.
Historien om bedriften startet like før årtusenskiftet.
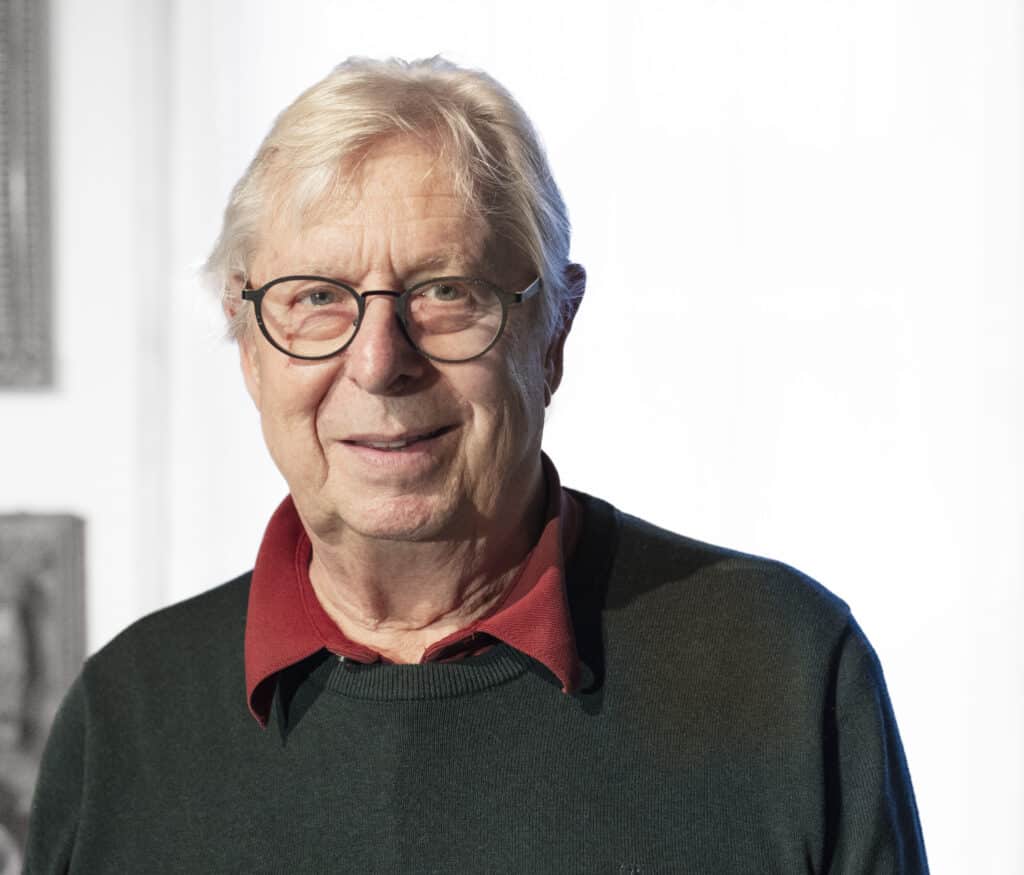
– Re-Turn ble etablert i 1998 for å lage en opptenningsbrikett som skulle bestå av bæreposeplast og treflis. Produktet het Re-Flame, og vi har gjort mange undersøkelser som viser at det er mindre farlig å brenne bærepose-plast enn det er å brenne ved og en rekke andre materialer. Mange tror imidlertid at det er farlig å brenne all plast, men et par av de vanligste plastmaterialene brenner meget rent, sier Stein Dietrichson.
Maling for skip
Han ble utdannet plastingeniør i 1973 i Østerrike. Interessen for plast var ikke tilfeldig med en far som var sjef på Norges første plastfabrikk NTP og en bestefar som var teknisk direktør på Helly Hansen, og som fant opp moderne regnklær.
Dietrichson jobbet i mange forskjellige firmaer før han startet for seg selv.
– I en alder av 53 år begynte jeg for fullt for meg selv i Re-Turn. Tennbrikettene ble lagt i skuffen, men vi jobbet videre med andre produkter. En gammel bekjent var spesialist på maling teknologi, så vi begynte å utvikle «Advanced Marine Coatings» (AMC), med nanomodifisert maling for skip. Samtidig fikk vi en del spennende oppdrag for offshore-sektoren, og etter hvert prosjekter med vindmøller. Parallelt gjennomførte vi en god del forskning, og beveget oss hele tiden i retning av mer miljøvennlig plast, nanoteknologi-lim og kompositter.
Ledende på plast-kompetanse
Grønne valg har vært en sentral del av Re-Turn hele tiden. Og de var tidlig ute med det meste.
– Mesteparten av det vi har drevet med har vi vært ti år for tidlig ute med. Timing har aldri vært min sterke side, smiler han.
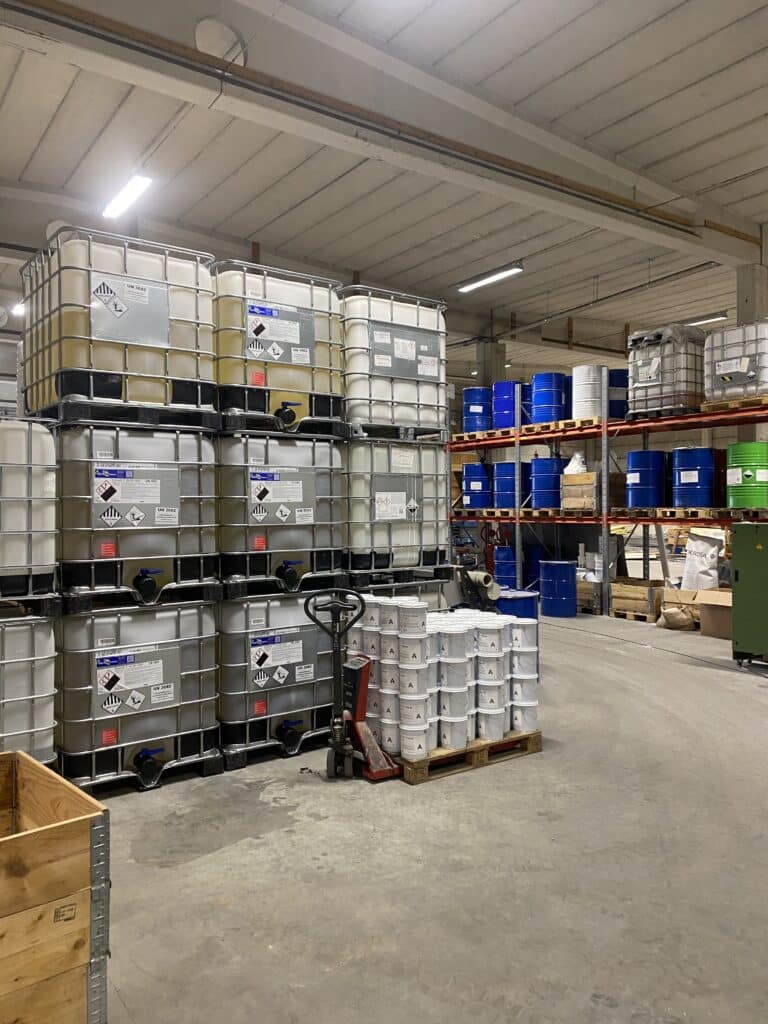
Kjernevirksomheten i Re-Turn er i dag produksjon av epoksy-systemer for maling, lim til byggevareindustri og småbåter mm. I tillegg har bedriften de siste 20 årene bygget opp et moderne laboratorium for testing av belegg, kompositter og termoplaster. Til sammen er seks personer ansatt i Norge, mens en jobber fra Stockholm.
– I den store sammenhengen er vi en mygg, men samtidig er vi et av de ledende kompetansefirmaene innenfor plast i Norge i dag. Laboratoriet vårt er ikke stort, men det er funksjonelt og kan konkurrere prismessig, sier han.
Nytt prosjekt
Gjennom årene har selskapet og Stein Dietrichson vært involvert i mange prosjekter og løsninger for resirkulering av polymere-materialer, inkludert innblanding av biobaserte materialer. Nå er han fagansvarlig for det nystartede prosjektet Thermo Plastics Circle – TPC. Prosjektet skal blant annet undersøke monoplast avfallsstrømmer og finne samarbeids- og logistikkløsninger for disse. Det skal også kartlegge hvordan lukt fra plastsøppel kan reduseres og optimalisere egenskaper ved den resirkulerte plasten, slik at plastprodusentene ikke opplever produksjonsstans og reklamasjoner.
Prosjektet er støttet av Handelens Miljøfond og Innovasjon Norge. Prosjektet eies og ledes av Norsk senter for Sirkulær Økonomi NCCE og i tillegg til Re-Turn og søsterselskapet Nordic Polymer & Processing Technology (NP&PT) er Borg Plast- Net (BPN), Beform, Bewi og Rotostøp med i prosjektet.
I dag går det meste av gjenvinnbar plast i Norge til eksport eller direkte til forbrenning. Omtrent syv prosent blir igjen til resirkulering i Norge.
– Vi tenker så kortsiktig i Norge at vi sender all plasten ut av landet. Plasten er en ressurs og den kan omdannes til noe fornuftig i Norge. Når oljeproduksjonen blir nedtrappet må vi alle bruke resirkulert plast, og da må vi kunne gjøre dette i Norge. Vi må slippe å importere plast som er resirkulert av plasten vi selv har levert, sier Stein Dietrichson.
Vil ta vare på ressursene
– Det viktigste med prosjektet er å finne ut hvordan disse ressursene kan tas vare på. Jeg besøkte nettopp et sykehus i Oslo hvor de sier at de har fått garanti for alle plastkannene de sender fra seg blir resirkulert. Men de blir ikke resirkulert i Norge, sier han.
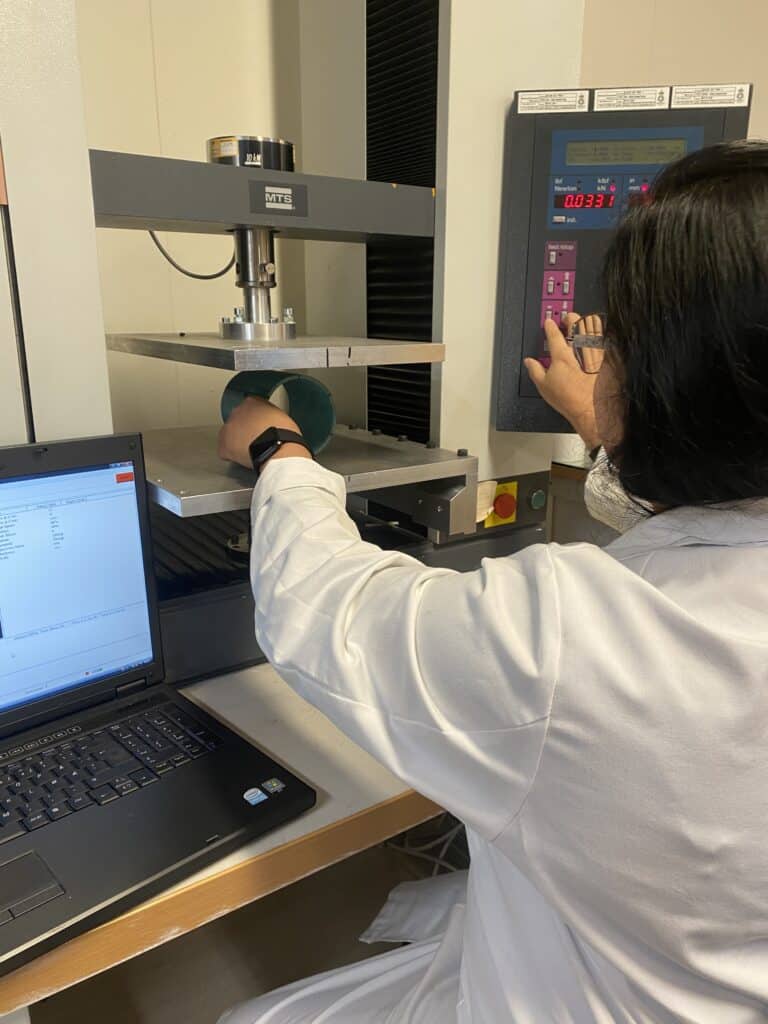
– Myndighetene har sagt at vi har så lite plastvolum i Norge at vi heller eksporterer det som et problem i stedet for å bruke det som en ressurs. Vi genererer mer enn 120.000 tonn plastavfall bare fra emballasje i året i Norge. Hvis myndighetene hadde ønsket det, kunne vi fint ha laget et resirkuleringsanlegg. Men økonomien i det å resirkulere plast er vanskelig. Det er dyrere å resirkulere enn å bruke jomfruelig plast, sier han.
Alle deltakerne har store forventninger til prosjektet.
– I Re-Turn og NP&PT har vi jobbet med dette i mage år, og har hatt noen forprosjekter. Og prosjektet bygger på en solid plattform av erfaringene og den kompetansen vi tilegnet oss. Nå får vi også den nye kompetansen som vi trenger. Vi tror både norsk plastindustri og brukere av plast vil få nytte av dette, sier han.
– Med kompetanse og fornuft kan plast leve evig. Det gjelder bare å se mulighetene, fastslår han.
Gir vindmølleblader nytt liv
Også utenfor Re-Turn har Dietrichson spennende prosjekter på gang. Sammen med en tidligere kollega har han blant annet jobbet med å lage terrassebord av treflis og plast. Da det viste seg at Norske Skog Saugbrugs jobbet med noe lignende, ble de to fagkonsulenter for dem.
Et annet pilotprosjekt er å sage opp vindmølleblader for å omdanne til lastbærende byggematerialer. Sammen med Pål Francis Hansen og tre andre har han startet Wingbeam AS.
– Vindmøllevingene lever ikke lenge. De eldre, små turbinene tas ned etter 10-15 år, mens de nye som settes opp nå varer i ca. 25 år. Vindmøllebladene er meget sterke siden de skal stå imot mye vær og stormer. Når de tas ned så har de til i dag ikke hatt noen fornuftige anvendelsesområder med større volumer, sier han.
Vindmøllebladene er laget av epoksy eller polyester forsterket med glassfiber og karbonfiber og inneholder mange verdifulle materialer i tillegg til plast, blant annet kobber og syrefast stål
– De materialene vi skal ta ut kan brukes i miljøer hvor det er mye korrosjon: Der stål vil ruste eller tre vil råtne. På den måten kan disse materialene fra vindmøllene brukes i alt fra brygger til pæler, og i anvendelser i oppdrettsanlegg, i bjelker og andre lastbærende konstruksjoner. Det kan erstatte stålbjelker og limtrebjelker. Vi har 3-4 patenter som er under utarbeidelse og dette har blitt veldig spennende, sier han.
Støtter NCCE
Han var også sentral da NCCE ble grunnlagt.
– Jeg sto på talerstolen på Øra-konferansen for en del år siden og avsluttet mitt innlegg med at det var på tide at vi lager et senter for sirkulærøkonomi i Fredrikstad. Etterpå hadde vi en del møter og fikk til den første finansieringen slik at vi kunne starte opp. Vi støtter opp om NCCE og ser det som viktig at det er noen som satser på sirkulær økonomi, sier Dietrichson som også var initiativtager til Borg Plast Nett for 20 år siden.
– Har du noen gode råd til andre som har en god ide innenfor sirkulær økonomi og vil starte opp?
– Det er viktig å tenke volum og stort, men å begynne forsiktig når finansieringen er på plass. De to første årene vil man helt sikkert ikke tjene penger. Jeg vil også anbefale å samarbeide med NCCE. Å melde seg inn for å få råd og hjelp, avslutter Stein Dietrichson.
Følg Re-Turn her: